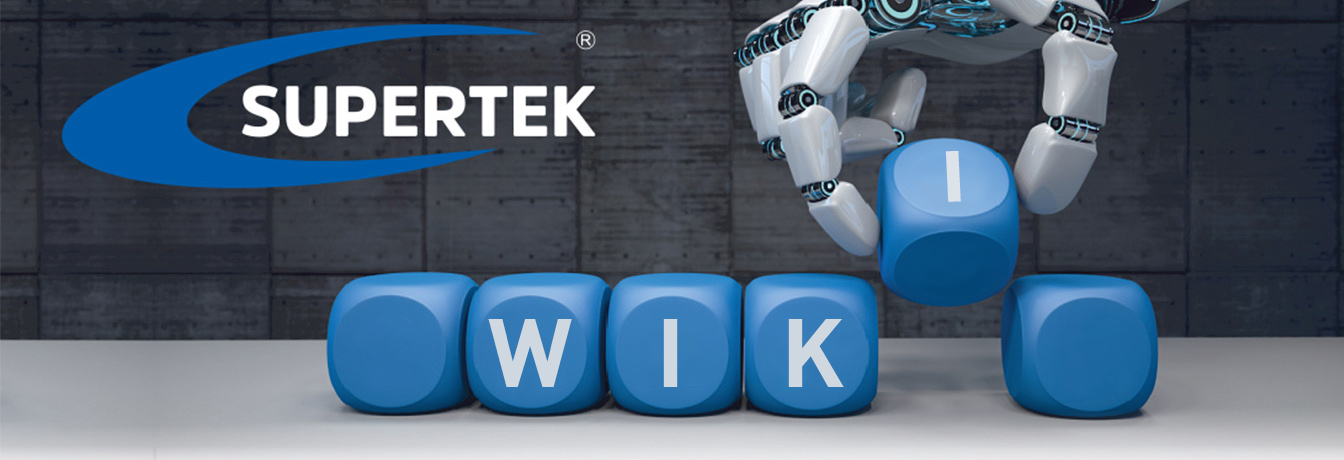
Methods of Tensile Force Controll
Depending on the requirements, cost-effectiveness, and technical feasibility, there are various methods to control the tensile force in a manufacturing process.
The tensile force of the material or the wound product must be precisely adjusted for a processing operation, such as rewinding, stranding, or coating wires. The fundamental requirements of tensile force control are illustrated here using an application example in the form of a simple wire rewinder.
On the left side of the upper illustration is an unwinder, and on the right side is a winder.
The tensile force must be such that optimal guidance of the wire is ensured. Too little tensile force on the wire leads to poor winding layers or the wire slipping off the guide rollers, causing the process to stop. Conversely, if the wire is stretched to the point of breaking, the tensile force is too high.
These two extremes illustrate that the tensile force must be adjusted not only to the processing operation but also to the physical properties of the product being used. For the optimal processing of the material, the requirements for tensile force control are significantly higher: the damping property of an optical fiber changes with variations in tensile tension.
To ensure consistent quality of the optical fiber, the tensile tension must be kept constant during processing.
Tensile force fluctuations lead to poor quality of the wound material and must therefore be prevented.
During the rewinding process, various parameters change, such as the spool diameter and, consequently, the unwinder's rotational speed. Regardless of these changing variables, the tensile force control should be able to maintain a constant tensile force. Another requirement is determined by the wire's line speed. The more rapidly the line speed changes, the more dynamically the tensile force control must be able to operate.
The methods of active tensile force control are:
- Drive control with force sensors
- Dancer position control
- Torque control