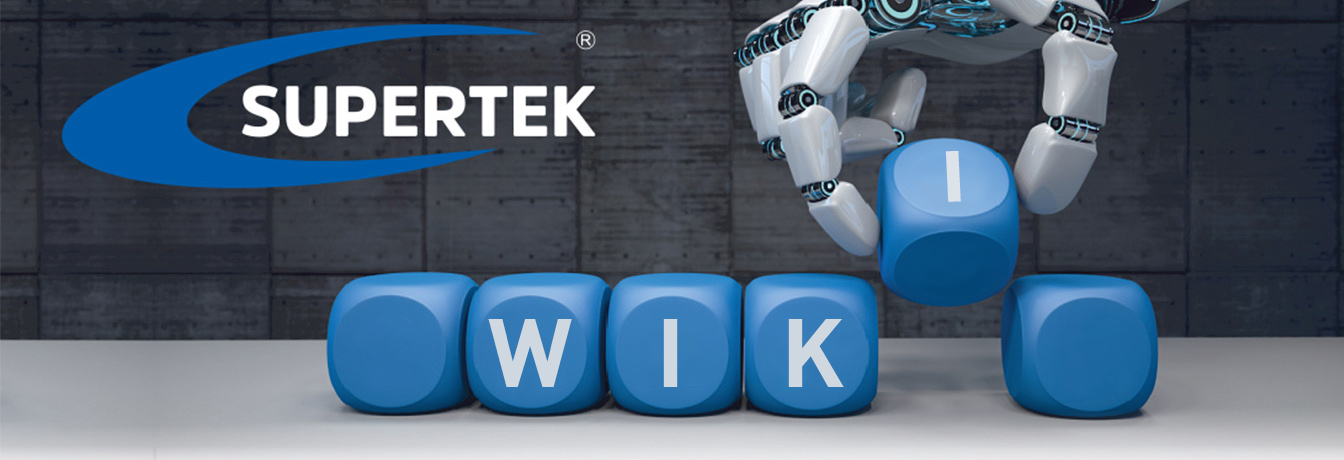
Dancer Control
Dancer control, also known as dancer position control, is a proven method for regulating the tensile stress or tensile force of spoolable materials using a dancer. Spoolable materials include wire, cable, fiber, filament, yarn, paper, or film.
The goal of dancer control is to maintain the tensile stress of the material at a constant level during drawing or winding. The unwinder, puller, or winder that needs to follow a material speed with a predetermined tensile stress is regulated using the dancer. An electric drive (motor) is used as the actuator, with speed as the control variable.
The tensile stress is primarily determined by the dancer force of the dancer, which acts on the material with a dancer roller. The dancer roller is mounted on a pivotable dancer arm or a linear guide, allowing the roller to change position and orientation. The dancer position or dancer orientation of the dancer roller is the control variable, measured with a sensor in the control loop. A position sensor or an orientation sensor, which outputs the dancer's position as a digital or analog signal (e.g., 0-10V), is used to measure the dancer's position.
The setpoint is the average dancer position (e.g., 5V) and corresponds to the control target. The actual position of the dancer is the actual value, so the difference between the setpoint and the actual value is the control deviation. The control deviation is ultimately determined by the difference in the material speed before and after the dancer roller. Ideally, the controller is designed so that the dancer roller moves to and remains at the middle position by adjusting the speed. A suitable controller for dancer control is the PID controller.